Media Centre
Robot palletiser head redesign provides a quick solution for a food manufacturing plant saving resource and energy costs
Our customer operating in the food manufacturing sector was experiencing problems with their pick and place robot failing to give the necessary accuracy of multi-box placement. The issue resulting in our client having to use resource for hand stillage labour so they requested an urgent solution. The original equipment manufacturer quoted several weeks to provide a copy head only.
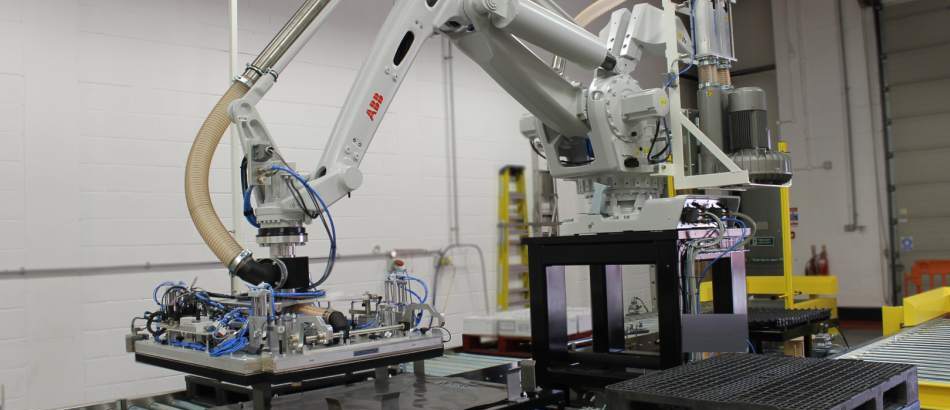
During a site visit by Advantiv engineers, the problem was identified as of a lack of controlled suction through the main vacuum head.
Solution
Our recommended solution was to re-design the head so that several sizes and orientations of boxes could be accurately picked rotated and placed in specific patterns on a storage pallet. Our solution included a non-marking, suction and discharge system, designed, developed and manufactured using products from the Piab product range and the experience of our engineering team and pneumatics system builder.
During the design phase we also identified an opportunity to improve energy efficiency and reduce the air consumption, which was achieved using a highly efficient Piab vacuum generator. This enabled a reduction in the number of suction cups and control of the air flow which subsequently cut air usage by ~75%. This reduction consequently reduced energy consumption and helped to improve the life expectancy of the main compressor system which was reaching its maximum output.
Outcome
The entire solution from the first site visit including design, manufacture, installation and commissioning took place over a period of 2-3 weeks, an improvement by some 3 weeks on the original equipment manufacturers lead time for a direct copy head.
Total saving to our client of ~£20k in hand stillage labour alone, over and above the ongoing energy saving.